When UAB ECSO, a company specializing in secondary raw material collection and sorting, noticed inefficiencies in their warehouse operations, they knew they had to act. Long truck waiting times and congestion around loading ramps affected their overall performance.
This case study delves into how ECSO leveraged GoRamp's Warehouse Management System (WMS) to streamline its operations, resulting in a 20% increase in loading capacity and a 40% reduction in driver wait times.
Founded in 2009, UAB ECSO, a pellet-production firm, began as a small enterprise focused on collecting secondary raw materials and prepping them for sorting. The company then spread its wings, expanding its activities and partnering with markets in Poland, Latvia, Estonia, Russia, and Belarus, among others. Openness to innovation and a strong focus on product quality are core values at ECSO.
Identifying the roadblocks
ECSO knew their warehouse was not up to snuff. The sight of queued-up trucks around their premises was a common occurrence. Because of that, incoming drivers had to spend more time waiting for their turn to park up in front of a ramp.
Naturally, anxiousness regarding penalties became apparent as everything took more time than anticipated. The primary issues they had to grapple with included:
- Truck congestion: Trucks were often queued around loading ramps, creating bottlenecks.
- Time delays: Drivers had to wait for an unreasonably long time before they could park at a ramp.
- Resource constraints: Limited resources were available for each loading point, making it challenging to speed up operations simply by increasing manpower.
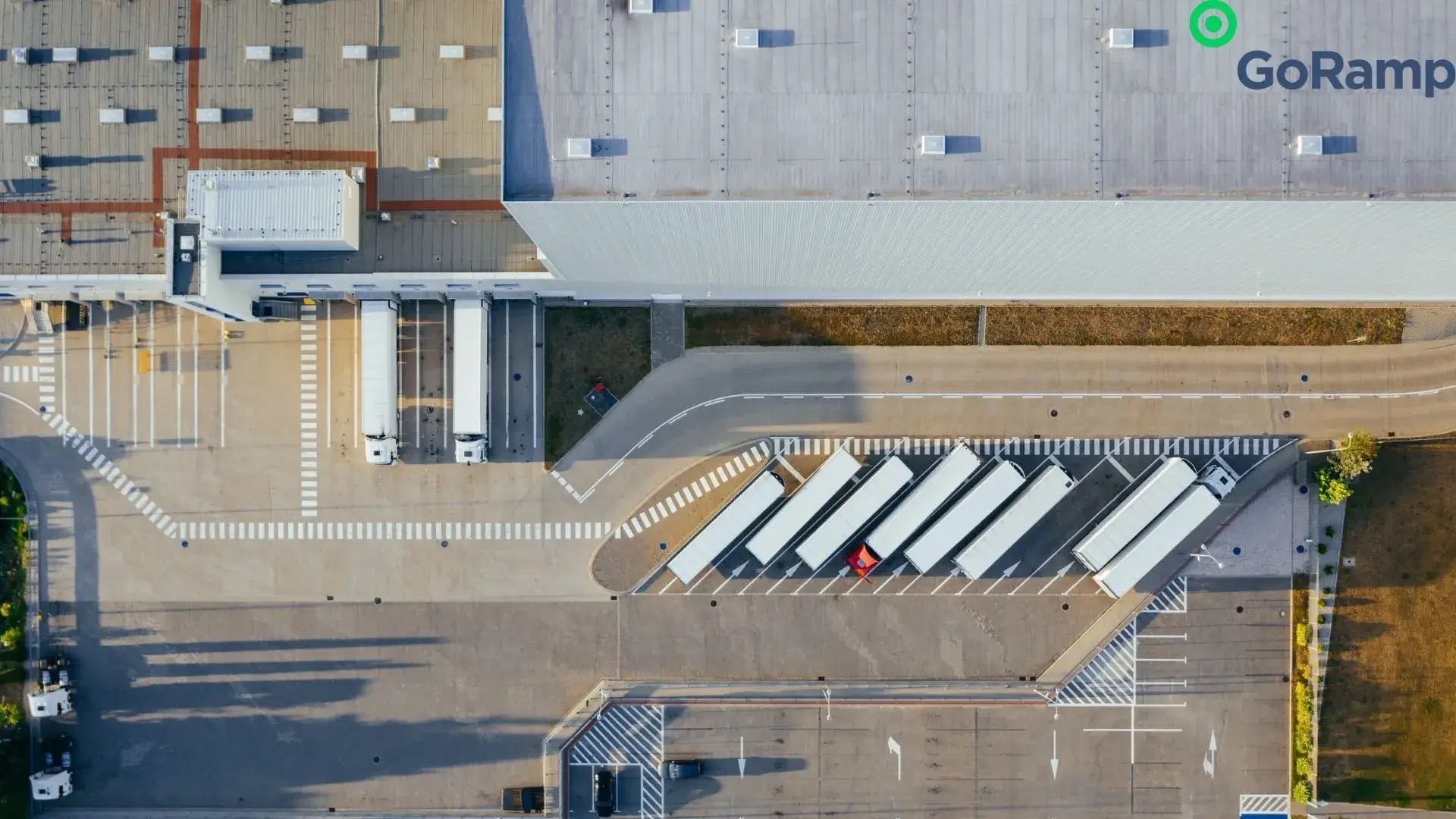
The tool of choice: Time Slot Management System
After careful consideration, ECSO chose to implement a Time Slot Management System to streamline their operations.
According to Justė Prunskienė, Business Development Manager for ECSO, they needed a system that made it easy to visualize how many trucks they were expecting and plan the arrival accordingly.
ECSO chose GoRamp's Time Slots Management System as their solution. The system allowed them to optimize their warehouse operating hours by considering existing limitations.
It provided incoming trucks with only serviceable periods to choose from, ensuring that the workload did not exceed the warehouse's capabilities. Moreover, the system centralized all required information, further streamlining the logistics process.
Immediate impact: Efficiency and communication
The improvements were noticeable right from the start. Employees could now access all relevant details in one place, which made their jobs easier and improved communication within the team. This reorganization of warehouse operations led to a 20% increase in their loading capacity.
Long-term benefits: Reduced waiting times and increased loading Capacity
The most significant impact was on the drivers. Their waiting time was reduced by 40%, allowing them to breathe easily upon arrival. The loading capacity also saw a 20% increase, which was a direct result of the newly implemented WMS.
ECSO's partnership with GoRamp has not only improved their current operations but has also set the stage for a long-lasting relationship. Both companies share a common goal—to provide customers with the best quality product. Implementing a WMS may not be easy, but ECSO's success story proves that it's possible and highly beneficial.
Book a free demo to see how GoRamp can help your business too.