How do you view your warehouse processes? How much time do you spend thinking about them? Your answer is important as it may reveal how much you are gaining or wasting through your warehouse operations.
Warehouse processes involve much more than knowing how goods move in and out - and packing them together in storage. It’s grasping the intricate network of activities that turns your warehouse into a powerhouse of efficiency and reliability. Every capable warehouse operator knows that the processes themselves are assets to the business—like a secret sauce or formula.
This article will unpack the critical role of ten strategic warehouse processes in optimizing your supply chain and explore how streamlining these elements elevates your entire operation.
1. Inventory management process
Inventory management encompasses stocktaking, inventory classification, and inventory turnover. Accurate stocktaking ensures you know what's on hand, while classification helps prioritize goods based on factors like demand and shelf life. Inventory turnover measures how often stock is sold and replaced, providing insights into sales performance.
Optimize inventory management
Streamlining inventory management can reduce holding costs, improve cash flow, and better responsiveness to market demands. It can also minimize stockouts or overstock situations, thereby enhancing customer satisfaction.
2. Order fulfillment process
Order fulfillment is a multi-faceted operation that goes beyond simple picking and packing. It involves meticulously selecting the right items, packaging them securely, and coordinating with various shipping partners to avoid late deliveries. The management of returns is another critical aspect, requiring a seamless process to handle product returns and refunds.
Optimizing order fulfillment
By leveraging technologies like automated sorting and real-time tracking, you can significantly reduce the time and errors associated with order fulfillment. This enhances customer satisfaction and allows for better labor allocation and tighter cost control.
3. Storage location and space optimization processes
Effective storage is a science that involves strategic slotting of items, optimizing the warehouse layout for maximum efficiency, and making seasonal adjustments to adapt to inventory fluctuations.
Optimizing storage location and space
Employing data-driven strategies for storage optimization can significantly reduce retrieval times and improve overall warehouse efficiency. This, in turn, lowers operational costs and speeds up order fulfillment, making your warehouse operations more competitive.
4. Real-time tracking and automation processes
Real-time tracking and wms automation are integral to modern warehousing. Utilizing RFID and barcode scanning technologies, Automated Guided Vehicles (AGVs), and integrating these with a Warehouse Management System (WMS) provides a centralized control mechanism.
Optimizing tracking and automation
The implementation of real-time tracking and automation technologies can drastically reduce manual errors, enhance workforce productivity, and provide actionable insights into warehouse operations, enabling better decision-making.
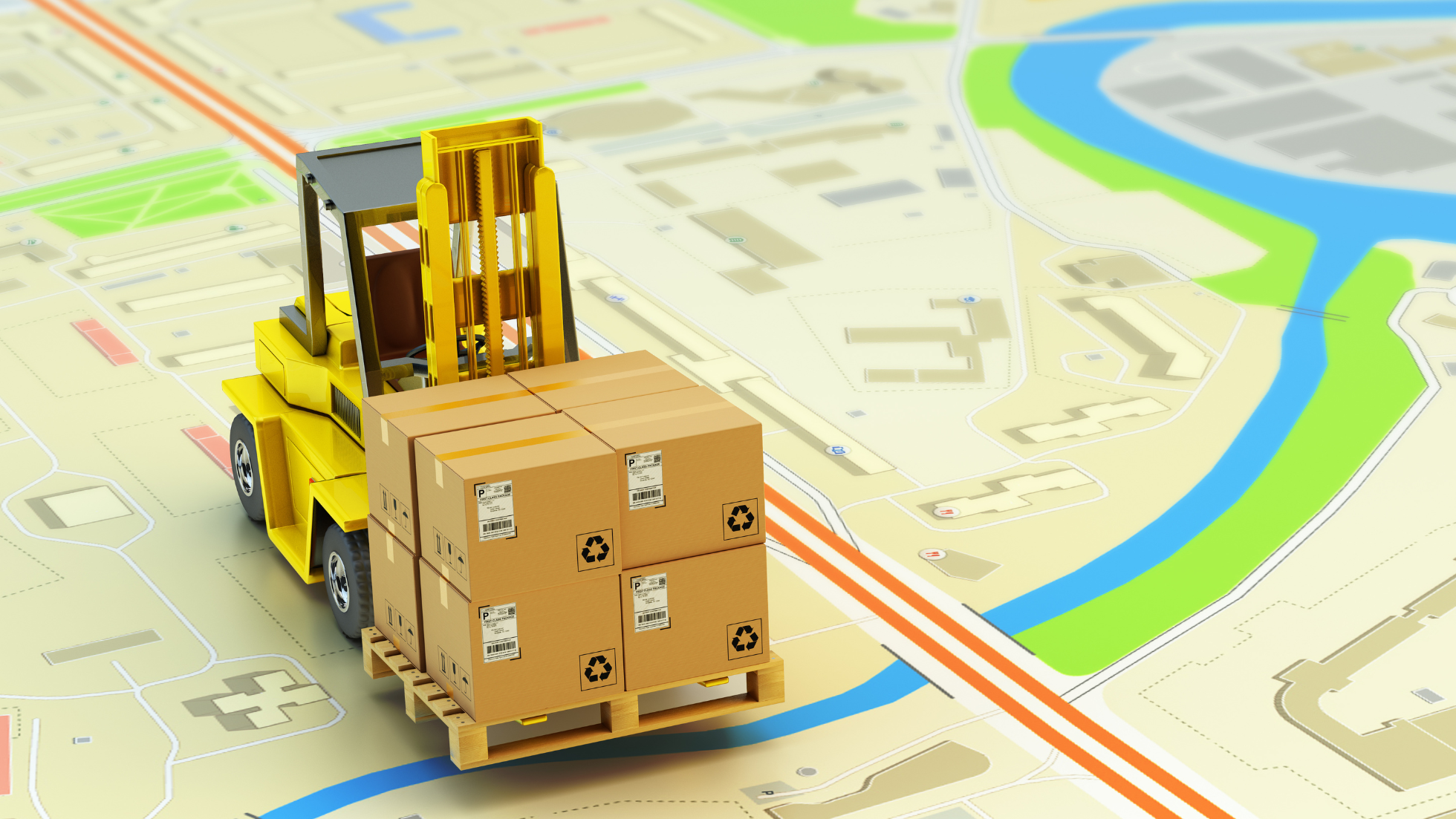
5. Quality control processes
Quality control is an ongoing process that involves multiple checks, including goods inspection, damage control measures, and compliance checks to ensure products meet or exceed established standards.
Optimizing quality control
A stringent quality control process can mitigate the risk of costly product recalls, enhance brand reputation, and ensure compliance with industry regulations, contributing to long-term business sustainability.
6. Inbound and outbound logistics
Inbound and outbound logistics cover the gamut of receiving goods, proper storage, and the organized loading and shipping of products. Each step is meticulously planned to maintain a smooth flow of goods.
Optimizing inbound and outbound logistics
Streamlining these logistics through advanced scheduling systems and real-time tracking can significantly reduce dwell times, improve inventory accuracy, and foster better relationships with suppliers and customers.
Find out how you can optimize your logistics with this complete guide to logistics in manufacturing.
7. Labor management processes
Labor management is a comprehensive system involving task allocation based on skill sets, productivity tracking through KPIs, and ongoing training and development programs for staff.
Optimizing labor management
Effective labor management strategies can lead to higher employee satisfaction, reduced turnover rates, and increased overall productivity, translating into significant cost savings.
8. Key performance indicators for measurement
KPIs are more than just performance metrics; they are the pulse of the warehouse. Metrics like accuracy rates, throughput, and cost per order are critical for a comprehensive evaluation of warehouse performance.
Optimizing KPIs
Regular monitoring and analysis of these KPIs can lead to actionable insights for continuous improvement, helping to identify inefficiencies and areas for cost reduction.
9. Streamlining and optimizing processes
Streamlining involves a deep dive into workflow analysis to identify bottlenecks, inefficiencies, and areas for improvement. It's an ongoing process that requires regular audits and adjustments.
Optimization
Some management systems aggregate performance data and offer analytic-based action items to implement. However, employing lean methodologies and similar principles through knowledge-based analysis and design can lead to more efficient operations, reduced operational costs, and a more agile and responsive warehouse.
10. Safety and compliance processes
Safety and compliance are foundational to any warehouse operation. This involves implementing rigorous safety protocols, ensuring complete regulatory compliance, and conducting regular audits and assessments.
Optimizing safety and compliance
A focus on safety and compliance minimizes the risk of workplace accidents and legal repercussions and contributes to a more productive and harmonious work environment.
11. Put-away process
The put-away warehouse process is a critical step in the logistics and supply chain management system that involves the systematic placement of received goods into their designated storage locations. This process begins once goods are unloaded from inbound trucks and inspected for accuracy and quality. Utilizing advanced Warehouse Management System (WMS) technology, items are scanned and directed to specific locations based on factors like product type, size, demand, and optimal picking routes. Efficient put-away strategies not only maximize warehouse space utilization but also ensure quicker retrieval and reduced handling times during the picking process. By streamlining the put-away process, warehouses can significantly enhance operational efficiency, reduce labor costs, and improve overall inventory management, leading to higher customer satisfaction with on-time deliveries with accurate customer orders.
Optimizing the put-away process
In warehousing involves leveraging advanced Warehouse Management System (WMS) technology, barcode or RFID scanning for accurate tracking, and strategic warehouse layout designs. Prioritize high-demand items for easy access and utilize slotting optimization based on item characteristics. Training and cross-training staff ensure best practices, while real-time data and analytics help identify and resolve bottlenecks. Coordination with receiving process and picking processes is crucial, and adopting lean warehousing principles reduces waste.
How using GoRamp’s Management Software helps optimize your warehouse processes
In the complex warehousing landscape, a robust tool streamlining warehouse operations is invaluable. Enter GoRamp, a cutting-edge software solution designed to optimize your warehouse processes. With a proven track record and recognition as the Best Dock Scheduling Software in 2022, GoRamp stands as a leader in the field.
Features and capabilities
GoRamp offers a comprehensive suite of cloud-based system features to enhance warehouse efficiency. From real-time tracking and automation to advanced inventory management, the software is engineered to address the most pressing challenges in warehousing. Its capabilities extend to order fulfillment, quality control, and even KPI tracking, offering a centralized platform for all your warehouse management needs.
Practical implications and benefits
Implementing GoRamp can lead to tangible improvements in your warehouse ops. The software's real-time tracking capabilities eliminate manual errors, while its advanced inventory management features reduce holding costs and improve cash flow. Moreover, its focus on data analytics allows for continuous improvement, helping you identify inefficiencies and implement corrective measures.
The benefits of using a wms tool like GoRamp go beyond mere feature sets. The software is backed by 23 years of industry experience and has already been adopted in 20 countries, serving more than 200 satisfied customers. Its adaptability to customer needs and focus on continuous innovation make it a reliable choice for those looking to elevate their warehousing strategy.
Book a quick demo to get started.