Why Is A Warehouse Safety Checklist Essential?
The safety culture within a warehouse is crucial for ensuring compliance with safety standards and safeguarding employees against potential hazards. A warehouse safety checklist is instrumental in identifying and managing risks associated with hazardous items and equipment, thereby preventing accidents and injuries. Regulatory bodies like OSHA provide guidelines that must be adhered to, ensuring a safe warehouse environment.
Continuous improvement through regular inspections and updates to safety practices is essential to adapt to the ever-evolving warehouse environment. Implementing a thorough and tailored safety checklist allows warehouses to address potential safety hazards proactively, leading to a safer and more efficient workplace.
Key Elements of an Effective Warehouse Safety Checklist
An effective warehouse safety checklist should include several key elements to ensure comprehensive safety management. These elements encompass personal protective equipment (PPE), fire safety measures, and material handling equipment, among others. Although these are foundational items, the checklist should be supplemented with additional relevant items based on specific warehouse needs.
Considering the unique risks of each warehouse environment when tailoring the checklist enhances effective safety management. A robust checklist should be easy to follow and cover various types of risks, ensuring that all potential safety hazards are addressed.
Personal Protective Equipment (PPE)
Personal protective equipment (PPE) is a critical component of warehouse safety. Workers are required to wear hard hats to protect against injuries from falling objects. Other essential PPE includes high-visibility jackets, safety glasses, safety boots, and gloves, all of which protect employees from various hazards in the warehouse environment.
Employers must provide appropriate PPE to their workers to ensure adequate protection while performing their duties. Proper use of PPE complies with safety standards and significantly reduces injury risks, promoting occupational safety and a safer workplace.
Fire Safety Measures
Fire safety is a paramount concern in any warehouse. Regular inspections should check portable fire extinguishers, sprinkler systems, hoses, and fire alarms to ensure they are in working order. Effective sprinkler systems and proper ventilation are key fire safety measures that help control the spread of fire.
Emergency exits must be clearly marked with emergency signage, adequate lighting, and unobstructed to ensure employees can evacuate safely in case of a fire. Following OSHA guidelines for fire safety standards is crucial for maintaining a safe warehouse environment and preventing fire exits-related incidents. Additionally, proper lighting and emergency signs are essential for guiding individuals during an evacuation.
Material Handling Equipment
Material handling equipment plays a vital role in warehouse operations, and ensuring its safe use is crucial. Outlining forklift pathways and clearly identifying lane markings help enforce correct forklift usage, preventing accidents. Safe lifting practices should consider factors like load weight, handholds, and lighting to minimize risks in materials handling.
Regular maintenance of warehouse equipment not only prolongs its lifespan but also reduces repair costs and enhances overall safety when properly maintained. Maintaining equipment in good condition prevents malfunctions that could cause serious injuries.
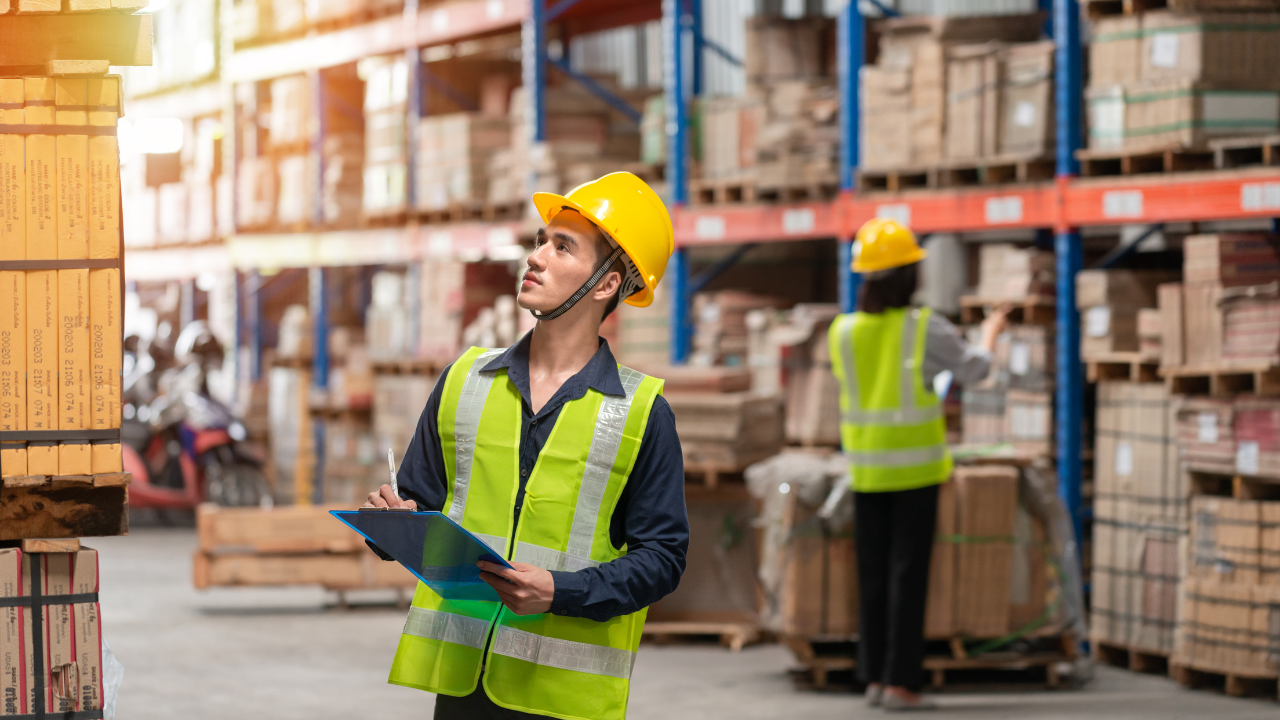
Conducting Regular Safety Inspections
Regular safety inspections help recognize potential hazards and ensure adherence to safety rules and regulations. Implementing safety procedures through a checklist can significantly reduce accidents in a warehouse setting. Regular maintenance checks are vital for upholding safety standards and creating a secure work environment.
Frequent inspections allow for the identification and correction of potential safety issues before they escalate. Maintaining a rigorous thorough inspection schedule ensures a safe and compliant operation, protecting employees and the business.
Routine Inspections
Routine inspections should occur every few weeks to every quarter to ensure safety compliance. Scheduling regular safety audit is crucial for maintaining OSHA regulations compliance and avoiding fines. Detailed audits should be conducted at least once a year to assess all safety parameters during an OSHA inspection.
Regular cleaning and addressing spills maintain dry and safe floors, reducing slip and fall incidents. Fire safety systems like extinguishers and sprinklers must be regularly inspected to ensure functionality. Frequent examinations of electrical systems are critical to prevent hazards such as shocks or fires.
Comprehensive Warehouse Safety Checklist
A comprehensive warehouse safety checklist includes detailed assessments of fire safety equipment, emergency procedures, and adequate ventilation. A thorough walkthrough of the warehouse safety inspection can be beneficial. It allows for the identification and recording of potential risks to take corrective action.
Complete and accurate warehouse inspection data is essential. It helps to ensure a safe working structure for warehouse staff. By maintaining thorough documentation and regular reviews, warehouse inspections can continuously improve their safety protocols and mitigate risks effectively. A comprehensive warehouse inspection report and an inspection template are crucial for this process.
Common Warehouse Safety Hazards and How to Mitigate Them
Warehouses are fraught with potential safety hazards, including fall risks, equipment malfunctions, and chemical exposure. Forklifts are particularly dangerous, leading to approximately 95,000 warehouse injuries annually, with fatal incidents often involving forklifts turning over. Improperly stored materials frequently cause workplace accidents, while environmental factors like low warehouse lighting and extreme temperatures add to the risks.
Providing proper training and ensuring regular maintenance are essential measures to train employees and protect workers from injuries related to conveyor belts and other equipment, especially when employees trained are involved in the operation.
Hazardous Chemicals
Proper storage and handling of hazardous chemicals ensure a safe working environment. Chemicals should be stored according to their classifications and regulatory standards to minimize health risks. Proper labeling with signal words, pictograms, hazard statements, and precautionary statements is essential for hazard communication.
Employees handling hazardous chemicals must be provided with the proper PPE and training. Employers must maintain and update Safety Data Sheets (SDSs) to inform users of the hazards associated with the chemicals.
Trip Hazards
Keeping walkways clear is essential to prevent accidents and ensure smooth operations. Unsafe walking surfaces can lead to slips, trips, and falls, making decluttering the warehouse a priority for warehouse workers and reducing any trip hazard.
Keeping floors and workstations free of clutter allows employees to move freely and safely around their work areas.
Electrical Safety
Regular maintenance of electrical equipment prevents malfunctions that could lead to electrical fires or shocks. Lockout/tagout procedures ensure electrical maintenance work is conducted safely and without accidental energization of equipment.
Proper training on electrical safety and emergency response is crucial for all employees working around electrical equipment. These measures help prevent accidents and ensure a safe working environment for everyone.
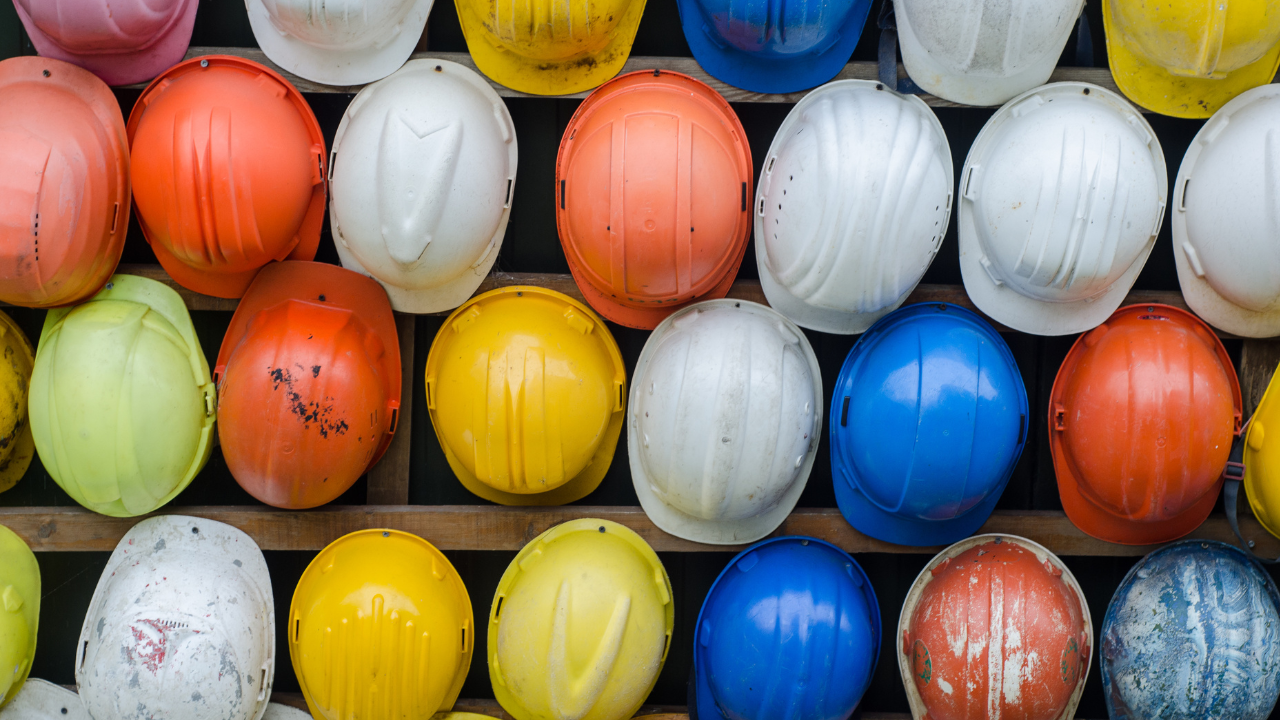
Training Employees on Warehouse Safety Procedures
Regular training keeps warehouse employees updated on safety protocols and ensures their well-being in the workplace. Employee training is essential, and every warehouse must have an emergency action plan guiding employees’ responses during crises, including clear evacuation procedures.
Employees should receive proper training in handling equipment, such as forklifts, which requires formal training and certification every three years to ensure safe operations. Creating and maintaining a comprehensive checklist ensures employees are familiar with safety protocols, greatly contributing to the overall safety of the warehouse.
Implementing Safety Protocols and Emergency Preparedness
Using a comprehensive safety checklist increases overall warehouse efficiency by preemptively addressing safety concerns. Safety drills enhance emergency response by allowing employees to practice their reactions to real-life scenarios in a controlled setting.
Regular safety drills foster a culture of safety by involving employees in maintaining a secure work environment. Drills help identify weaknesses in emergency response plans, allowing for improvements in protocols and warehouse layout.
Utilizing Technology for Improved Safety Management
Technology plays a crucial role in enhancing safety management by automating processes and providing real-time tracking. CMMS software helps manage, automate, and systematize maintenance operations, ensuring that safety protocols are followed diligently.
SphereWMS enhances warehouse safety by optimizing inventory control, streamlining workflows, and ensuring clear and organized storage. Integrating technology in safety management improves compliance and fosters a culture of proactive safety practices within the warehouse environment.
Summary
In summary, a comprehensive warehouse safety checklist is essential for identifying and managing potential hazards, ensuring compliance with safety standards, and fostering a culture of safety within the warehouse environment. Regular safety inspections, proper training, and the use of technology are all vital components of an effective safety management strategy.
By implementing these best practices and tips, warehouses can create a safer and more efficient working environment, protecting both employees and operations. Remember, a safe warehouse is a productive warehouse, and investing in safety measures is investing in the future success of your business.
FAQ
What is a warehouse safety checklist?
A warehouse safety checklist is essential for identifying potential hazards and ensuring compliance with safety regulations, helping to create a safer working environment. Regularly using this checklist can significantly reduce the risk of accidents and injuries in the warehouse.
Why is a warehouse safety checklist essential?
A warehouse safety checklist is essential because it identifies and manages risks, ensures compliance with safety standards, and promotes a culture of safety. Implementing such a checklist protects both employees and the overall operational integrity of the warehouse.
What are the key elements of an effective warehouse safety checklist?
An effective warehouse safety checklist should include personal protective equipment (PPE), fire safety measures, material handling equipment, routine inspections, and emergency readiness. By ensuring these key elements are consistently addressed, you can significantly enhance workplace safety.
How often should routine safety inspections be conducted?
Routine safety inspections should be conducted every few weeks to quarterly, with comprehensive audits at least once a year to ensure ongoing compliance and safety.
How can technology improve warehouse safety management?
Implementing technology can significantly enhance warehouse safety management through process automation, real-time tracking, and better adherence to safety protocols. This not only reduces risk but also fosters a safer working environment.