Moki-veži, a prominent retail and wholesale chain in Lithuania, faced a big challenge during its growth phase. With an expanding network of 24 stores in 20 cities and over 750 employees, the company was struggling with challenges in its warehouse operations.
These challenges included long truck waiting times, inefficient scheduling, and poor communication among the warehouse staff, suppliers, and carriers.
As delivery volumes increased, the need for a smarter approach to manage these issues became evident. It was clear that adding more resources wasn't the solution; the focus needed to shift to making their processes more efficient.
The Digital Solution: Adopting GoRamp
The introduction of GoRamp's Warehouse Management and Dock Scheduling System marked a turning point for Moki-veži. Audrius Aleksandravičius, the Head of the Supply Group, saw the potential in digital solutions to transform their supply chain management. The goal was to utilize existing resources better to improve business outcomes without increasing the workforce or infrastructure. GoRamp offered a comprehensive solution that could address multiple facets of its warehouse operations.
"GoRamp has helped Moki-veži avoid inconsistent dock utilization, transportation queues, and chaotic communication between warehouse staff, suppliers, logistics departments, and carriers. By tracking the flow of deliveries in real-time, we can plan the schedule for loading and unloading in advance and arrange time slots for docking online." - Audrius Aleksandravičius, Head of Supply Group at Moki-veži.
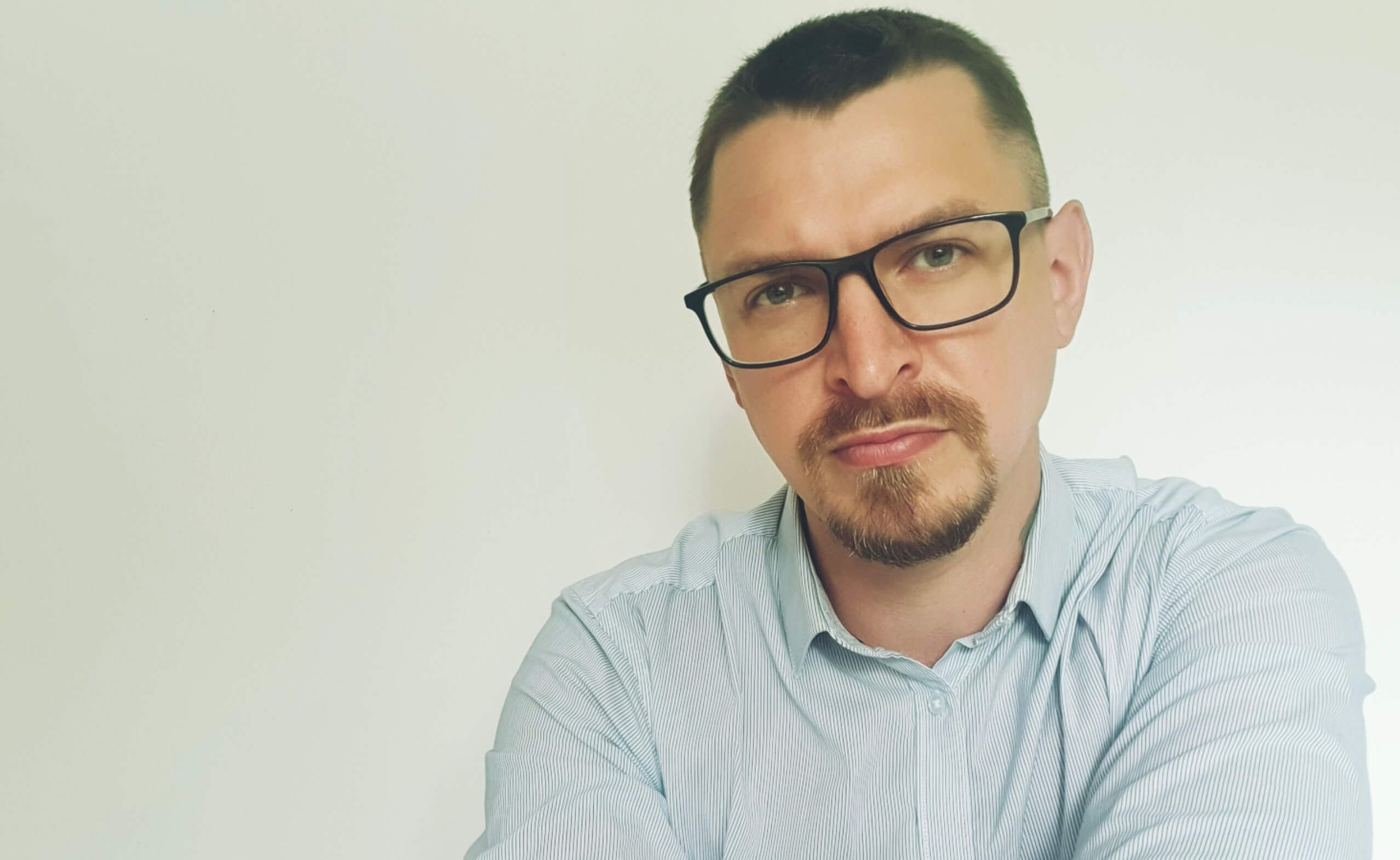
Implementing GoRamp brought immediate improvements. The system enabled Moki-veži to:
- track deliveries in real-time, which was a game-changer.
- plan for dock usage, significantly reducing the previously long wait times for trucks.
- communicate easily with stakeholders, eliminating the previous disorder and confusion.
Intuitive interface and data-driven decisions
One of the standout features of GoRamp was its user-friendly interface. The intuitive design meant that the Moki-veži team could quickly adapt to the new system without needing extensive training. This ease of integration was crucial in ensuring that the transition to GoRamp didn't disrupt their ongoing operations.
GoRamp didn't just streamline warehouse operations; it revolutionized how Moki-veži made decisions. With robust analytics and data at their fingertips, the management team could make informed decisions based on actual performance metrics. This shift to a data-driven approach was significant, as it allowed for continuous process improvement and strategic planning based on reliable data.
Are you considering a dock scheduling software for your business? Learn from the experiences of companies like Bauroc, Kompak, and Sakret, who have also enhanced their warehouse operations with GoRamp. Discover more about GoRamp's Warehouse Management Solution and see how it can revolutionize your business operations - book a call with us today!